From The Trail

2023 note: The sale of our trekking poles has moved over to our new brand Diorite Gear. Our trekking poles come with either EVA or Cork grips, which is a pretty common offer in the outdoor market. Usually the weight difference between...
Continue reading
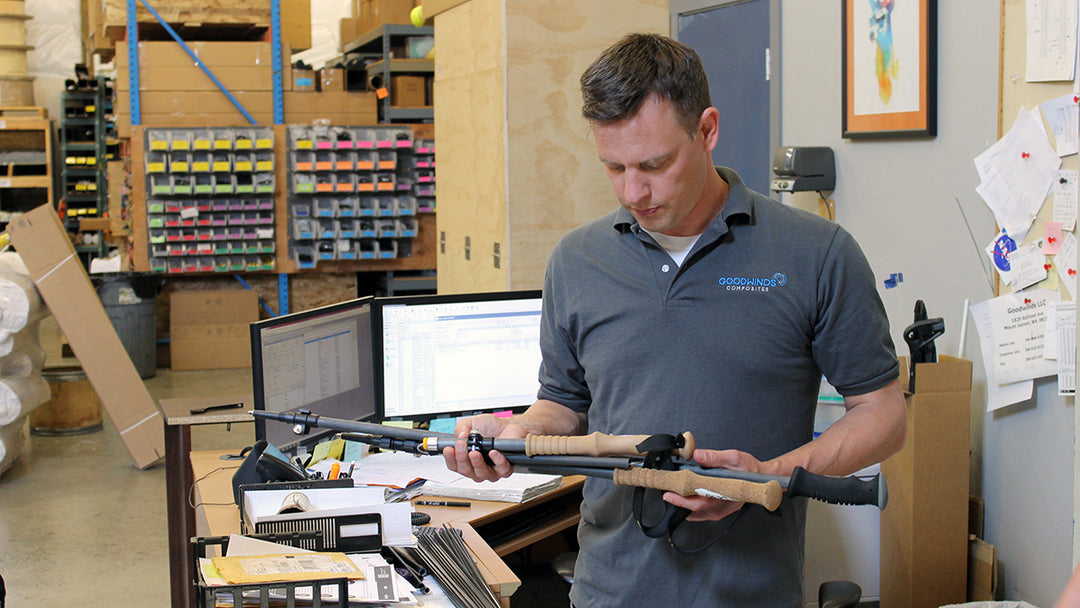
They helped NASA build a helicopter for Mars, but Goodwinds Composites is still a very down to Earth company. When we were looking for a US carbon fiber tube manufacturer for our Cnoc trekking poles, we knew we couldn't do better...
Continue reading